Siamo approdati, ma noi comuni utenti e consumatori forse non ce ne siamo accorti, alla quarta rivoluzione industriale; dopo la prima del 1784, quando furono introdotte, nelle aziende, le macchine a vapore; la seconda del 1870 che introdusse l’elettricità ed il petrolio e la terza del 1970 che ha introdotto l’informatica. Ora, come è stato constatato al Word Economic Forum di Davos dello scorso anno, comincia l’utilizzo di macchine intelligenti, interconnesse e collegate ad internet. “Connessione a sistemi fisici e digitali, analisi complesse attraverso Big Data ed adattamenti real-time”. Tradotto per noi comuni mortali, tra qualche anno ogni nostro oggetto, anche casalingo, uscito dalla produzione delle moderne aziende, sarà connesso con le aziende stesse che da remoto potranno seguirne l’utilizzo, verificare eventuali malfunzionamenti, segnalare il problema al riparatore, eseguire anche a distanza le modifiche necessarie al nostro apparecchio. Il vantaggio per le aziende sarà enorme, visto che esse potranno, attraverso il monitoraggio continuo degli apparecchi prodotti da esse stesse, modificare e migliorare la qualità dei materiali, il software di funzionamento, ottenere la migliore soddisfazione del cliente e, di conseguenza, minori costi di produzione e di quello finale sul mercato. Ha illustrato il tutto al Rotary club di Putignano lo scorso 7 settembre, Francesco Mercieri , socio dello stesso club, invitato dal presidente Nicola Paladino, per la relazione sul tema “Industria 4.0 – la quarta rivoluzione industriale”. Mercieri, che attualmente svolge attività di consulenza e di temporary management ed è membro della Commissione Nazionale Industria 4.0 di Federmanager, è un dirigente d’azienda con esperienza trentennale vissuta in varie aziende piccole e grandi, tra cui Bosch e Fiat; in queste ultime il suo notevolissimo know-how gli ha permesso la piena responsabilità tecnica ed economica e la gestione di modifiche organizzative e di ristrutturazione di interi siti produttivi. In qualità di Direttore di stabilimento, ultimamente ha gestito importanti lanci di prodotti strategici in aziende multinazionali, tra cui quello della Fiat 500X e della Jeep Renegade. Oggi dunque, che il processo di produzione si è evoluto, possiamo parlare di industria 4.0, in cui già si utilizzano informatizzazione e digitalizzazione nella catena produttiva, con tecnologia di avanguardia come i Big Data, il Cloud, e soprattutto “l’internet delle cose”, ogni macchina che produce ed ogni prodotto realizzato sono collegati tra di loro, producono e si scambiano dati, facendo in modo che la produzione possa autocontrollarsi. Mercieri ha fatto l’esempio dello stabilimento Lear Corporation di Melfi nel quale ogni 52 secondi viene “battezzata” una 500X (come dire, analizzata, esaminata, radiografata…) , sempre diversa una dall’altra, a seconda delle richieste del cliente e delle modifiche tecniche ed elettroniche apportate continuamente dell’azienda stessa: l’azienda che produce componenti, ad esempio sedili, sempre connessa, li produrrà di colore, forma, aerodinamica, funzionalità… sempre diversi, per incontrare il gusto del cliente finale e far trovare sempre pronta l’azienda madre. Come sarà dunque, la fabbrica del futuro? Essa avrà un controllo continuo della produzione; una rete di macchinari massimamente ottimizzanti; un sistema di manifattura altamente avanzato, con “l’internet delle cose”, installazione di “sensori”su ogni prodotto perché esso dialoghi con le macchine produttrici e con le stesse aziende; un utilizzo ed uno studio di una grande massa di dati, reso possibile con il loro immagazzinamento in “cloud computing” e con la massima attenzione alla cybersicurezza; una ricerca di massima soddisfazione del cliente sui prodotti di larga scala; un aumentato studio di ingegneria con la massima interfaccia uomo-macchina; un utilizzo di nanotecnologie e di materiali avanzati; la creazione di “smart products”, prodotti intelligenti che creino valore per il cliente; una progettazione virtuale, anche con la simulazione del prodotto; una produzione “additiva” con stampanti “3D”, utilizzo di “realtà aumentata” e di macchine-robot autonome; una “smart logistics”, tracciamento continuo del prodotto durante i suoi spostamenti e monitoraggio totale delle giacenze ed infine uno studio delle risorse future, soprattutto del vento e di quelle alternative non convenzionali, solari e geotermiche. Tutto ciò per assicurare la massima qualità e per ridurre gli sprechi. Molti governi da qualche tempo hanno elaborato piani nazionali a sostegno della digitalizzazione delle aziende.e della produzione manifatturiera: Germania, in primis; ma anche Francia, Gran Bretagna, Olanda, Stati Uniti, Cina, India, Giappone, Canada e Corea. In Italia il grado di conoscenza del problema è molto basso; il 38% non lo conosce affatto, il 28% ha letto qualcosa; il 13% sta valutando di fare qualcosa e soltanto il 15% ha introdotto soluzioni del tipo. Tra gli apripista nel settore troviamo come sempre la Germania e gli Usa, mentre l’Italia purtroppo si colloca tra gli “Hesitators”. Eppure una azienda del futuro permette una riduzione generalizzata dei costi di produzione, una aumentata qualità dei prodotti, un aumento della produttività, una riduzione del volume e del numero delle macchine, una diminuzione dei costi di mantenimento, una riduzione dei tempi di vendita, di giacenza e di inventario. Ipotizzando che la metà delle aziende europee nei prossimi vent’anni si adeguerà ai paradigmi della Industria 4.0, il nuovo modello porterà loro un aumento della redditività ed un uso più efficiente del capitale investito , generando nuove opportunità di investimento e modifiche del profilo della forza lavoro. In Italia, dunque, il Ministero dello sviluppo economico, guidato ultimamente dal ministro Carlo Calenda, con il Piano Industria 4.0 cerca di incentivare i privati ad investire su tecnologie e beni 4.0; di aumentare la spesa (sempre dei privati) in ricerca, sviluppo ed innovazione; di rafforzare il sostegno alle start-up; di garantire tali investimenti privati; di supportare lo scambio salario-produttività attraverso la contrattazione decentrata aziendale. Ma anche e soprattutto con la creazione di una adeguata rete infrastrutturale con l’estensione della banda larga (tutte le azienda coperte da trenta Mbps ed almeno il 50% entro il 2020 da 100 Mbps) e con la diffusione della cultura “I 4.0” attraverso lo sviluppo di percorsi universitari e di istituti superiori dedicati. Ma l’Italia “esita”. Eppure le cifre del piano non sono proprio piccole: 13 miliardi di incentivi fiscali, 10 miliardi di investimenti in più già nel 2017; incentivazione massima degli investimenti privati con superammortamenti ed iperammortamenti.. In Puglia lo stato di avanzamento di tale piano è in una buona fase di avvio, grazie al buon lavoro di Confindustria di Bari; come pure in Lombardia, Lazio e Marche. Mentre sono già in una fase operativa il Piemonte, il Veneto, il Friuli e l’Umbria. Male invece, sono nella fase di progettazione, Campania, Calabria, Liguria e Toscana. Eppure il Piano “I 4.0” sembra funzionare, visto l’aumento record di acquisto di macchinari, secondo una indagine de La Repubblica. . Ma questa rivoluzione è tutta positiva? Vista dalle fabbriche che già si sono adeguate al nuovo protocollo, la situazione è felice. Ma non è che l’estrema automazione (tra dieci anni i robot saranno autonomamente anche in grado di assistere le persone anziane), porterà ad una diminuzione dei posti di lavoro? Un imprenditore bresciano sostiene di avere oggi lo stesso numero di dipendenti di dieci anni fa, 360; con la variante che prima erano trecento operai e sessanta impiegati, oggi gli operai sono duecento e gli altri impiegati e soprattutto tecnici che controllano i processi produttivi e dall’Italia anche le linee di produzione in Brasile ed in India: “Non è diminuita l’occupazione, ma è migliorata la qualità del lavoro”. Ma il Fondo Monetario Internazionale imputa lo spostamento dal 1970 ad oggi di ben quattro punti di reddito nazionale dai lavoratori alle aziende. Secondo i ricercatori di Brueget, autorevole agenzia di Bruxelles, tra il 45 ed il 60% della forza-lavoro europea rischia nei prossimi decenni di essere sostituita dai robot; e secondo un rapporto della Mckinsey in tutto il mondo sono un miliardo e duecento milioni i posti sostituibili con le tecnologie. Secondo il gruppo di mamme in affari (“Business Mum”), per ogni posto di lavoro obsoleto perso, si creeranno 2,4 posti di lavoro nuovo e nonostante ci sia chi dice che presto i robot decideranno al posto nostro, grazie a questo nuovo processo le nostre competenze aumenteranno e cederemo i lavori più umili e faticosi alle macchine. Sempre tali mamme sostengono che, mentre la prima rivoluzione industriale aveva ridotto i salari ed obbligato gli operai a turni di lavoro estenuanti, con la trasformazione dell’artigiano in operaio, la quarta avrà effetti opposti in quanto avrà bisogno di persone altamente qualificate (e ben pagate) per inventare, gestire e manutenere tutte le innovazioni. Cosa dovremmo dunque far studiare ai nostri figli? Secondo le Businnes Mum e la stessa Commissione Europea, le lauree STEM, acronimo che sta per Science, Technology, Engineering and Mathematics. Scienze, tecnologia, ingegneria e matematica, le materie più temute dai nostri studenti, ma sicuramente le più utili in futuro. Cosa serve per stare al passo? Sicuramente una nuova cultura di impresa che ancora una volta metta l’uomo al centro della fabbrica , con competenze diverse e superiori a quelle attuali. Ed il Rotary? Il presidente Nicola Paladino ha spronato i vari imprenditori presenti nel club ad “osare” di più ed a “sfruttare” le opportunità che offre il Piano italiano, se questo si tradurrà in una maggiore e più qualificata occupazione dei nostri giovani.
Pietro Gonnella
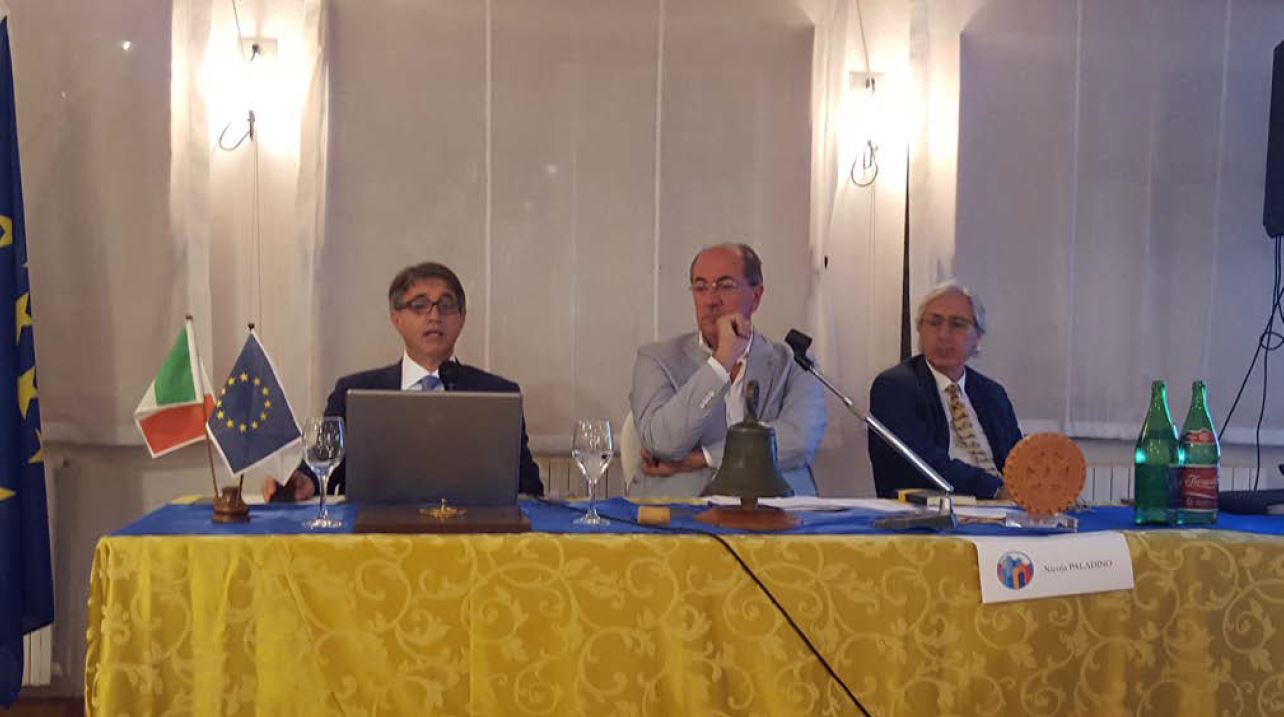
Notizie collegate